In the world of manufacturing, precision and performance are of the utmost importance.
Behind every on-time delivery, optimized supply chain, and satisfied customer stands a very important department: shipping/logistics. At Cordeck, our logistics team ensures that materials arrive on time, production schedules stay on track, and finished products reach their destinations efficiently and reliably. We interviewed members of our Logistics team to gain insight into the world of Cordeck logistics.
Logistics Role at Cordeck
Logistics plays a vital role in supporting Cordeck’s overall goals and customer service. The team takes a proactive approach to meet customer needs by scheduling timely delivery by Cordeck’s own fleet, securing a driver at the last minute, directly coordinating with carriers, coordinating shipping in and out of our 8 locations, or negotiating rates to keep delivery costs down. By doing everything they can to get materials to the job site on time, they help ensure projects stay on schedule and customers stay happy.
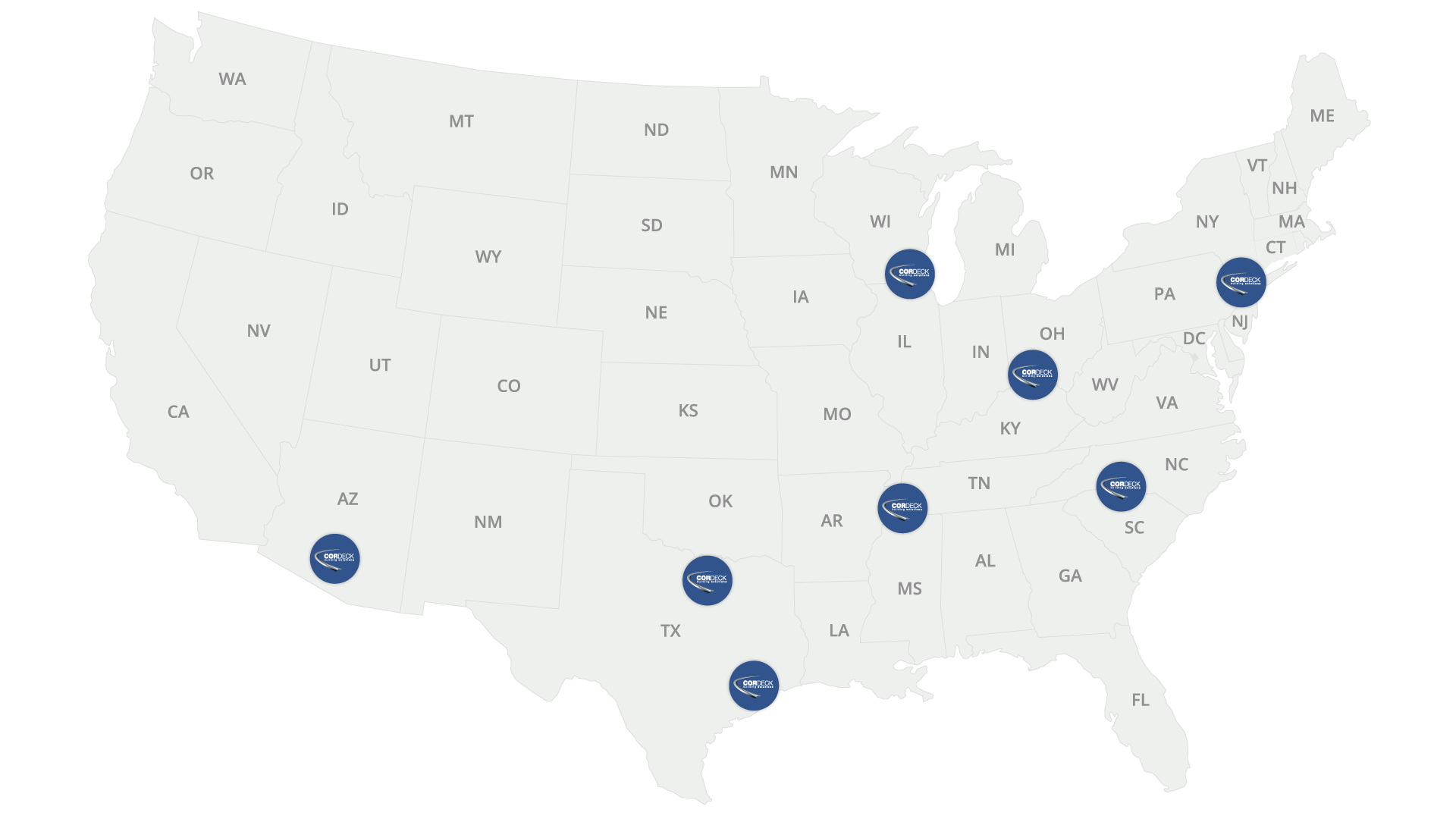
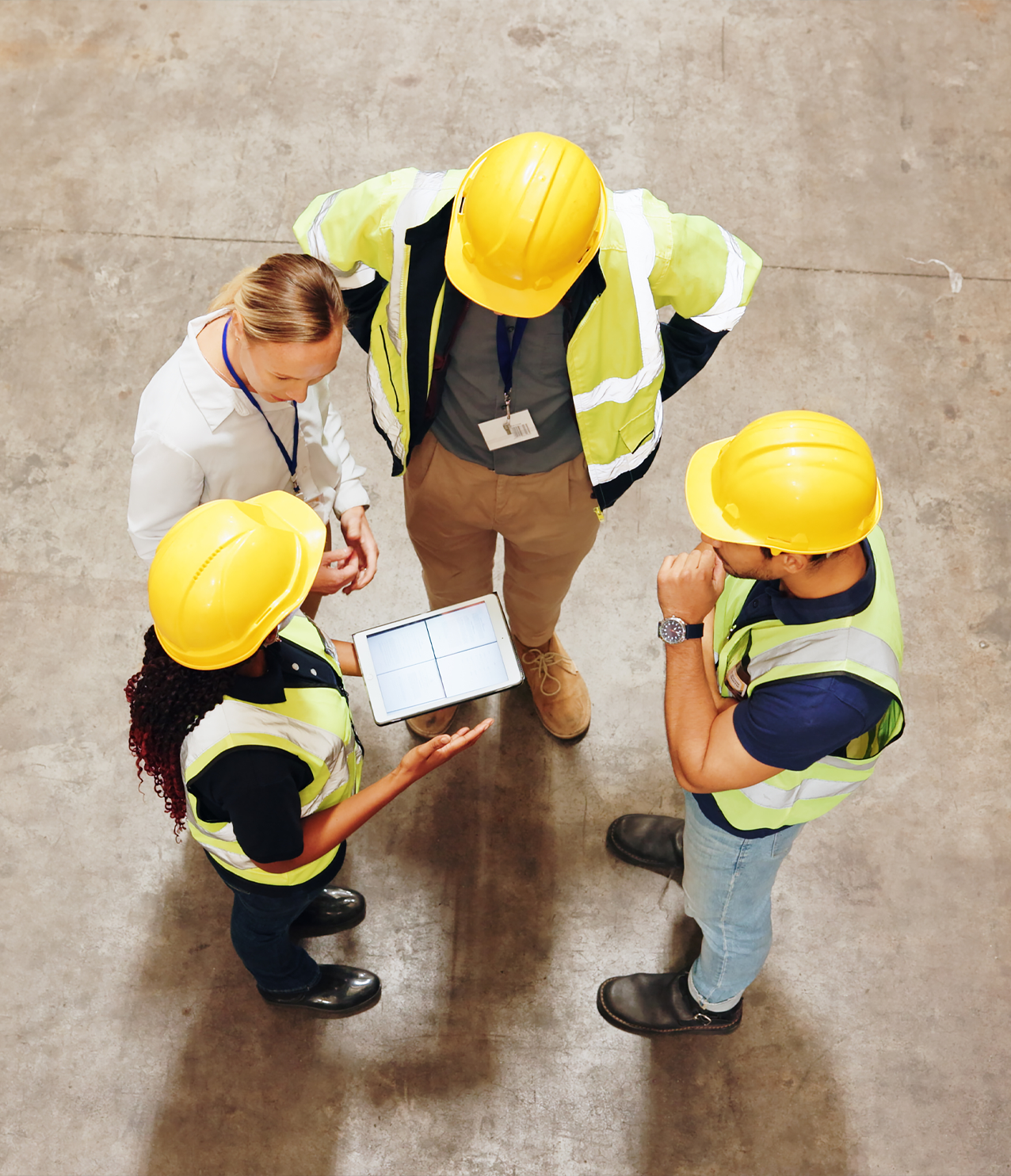
Order Fulfillment Process
Fulfilling a typical order is a very detailed and collaborative process. It begins with reaching out to the customer to confirm delivery expectations, verify address details, and establish a timeline. From there, the team coordinates delivery routes using Cordeck’s own fleet of trucks and negotiates with drivers and brokers to secure the best delivery solution that balances cost, timing, and reliability. Once materials are loaded and shipped, they obtain proof of delivery and manage any issues that arise, ensuring the job is done right from start to finish.
Our logistics team is very mindful with their shipping coordination. Our team makes sure that we are flexible and communicate effectively with customers, our own fleet, and third party carriers for arranging pickups and deliveries in a timely manner.
Tackling Supply Chain Disruptions
Supply chain disruptions and unexpected delays are part of logistics, but our team at Cordeck meets these challenges head-on. Open communication is key. The team keeps both customers and internal departments informed of any delays, often anticipating issues before they arise. By forecasting potential disruptions, they give everyone involved time to adjust and keep projects moving forward.
The Challenges with Timing & Last Minute Changes
Timing is one of the biggest challenges. Cordeck has built its reputation and business on quick turnaround and providing next day delivery. Consistent communication internally and with our customers is ongoing to ensure that customer expectations are met.
In logistics, no two days are the same. Last-minute changes and urgent requests are common and the team has learned to thrive in that environment. Strong communication with internal teams and external partners, along with the ability to lean on remote facilities when necessary, helps the department stay flexible and responsive under pressure.
Recent Logistics Success Story
One recent success story reflects the department’s dedication: our Traffic Coordinator Justin worked on the weekend to ensure a customer received critical materials on time. Not only did this effort keep the project on schedule, but it also saved the customer money by consolidating multiple deliveries on the same truck.
Continuous Process Improvements
As the logistics space continues to evolve, so does the team at Cordeck. They adapt quickly, creating new processes and embracing change to meet the company’s shifting needs. One major improvement over the past year involved fixing the communication process with key customers. By calling ahead to confirm jobsite readiness before materials are dispatched and implementing a structured email follow-up, the team has continuously prevented unnecessary deliveries, improved inventory accuracy, and enhanced customer satisfaction.
A new communication process has been implemented to ensure jobsite readiness prior to material delivery for our customers. By proactively calling ahead, we make sure that the site is ready to receive the materials, which helps prevent unnecessary shipments. This approach not only streamlines operations but also supports more accurate inventory management. Additionally, an email confirmation process is in place to reinforce this system and minimize the risk of miscommunication.
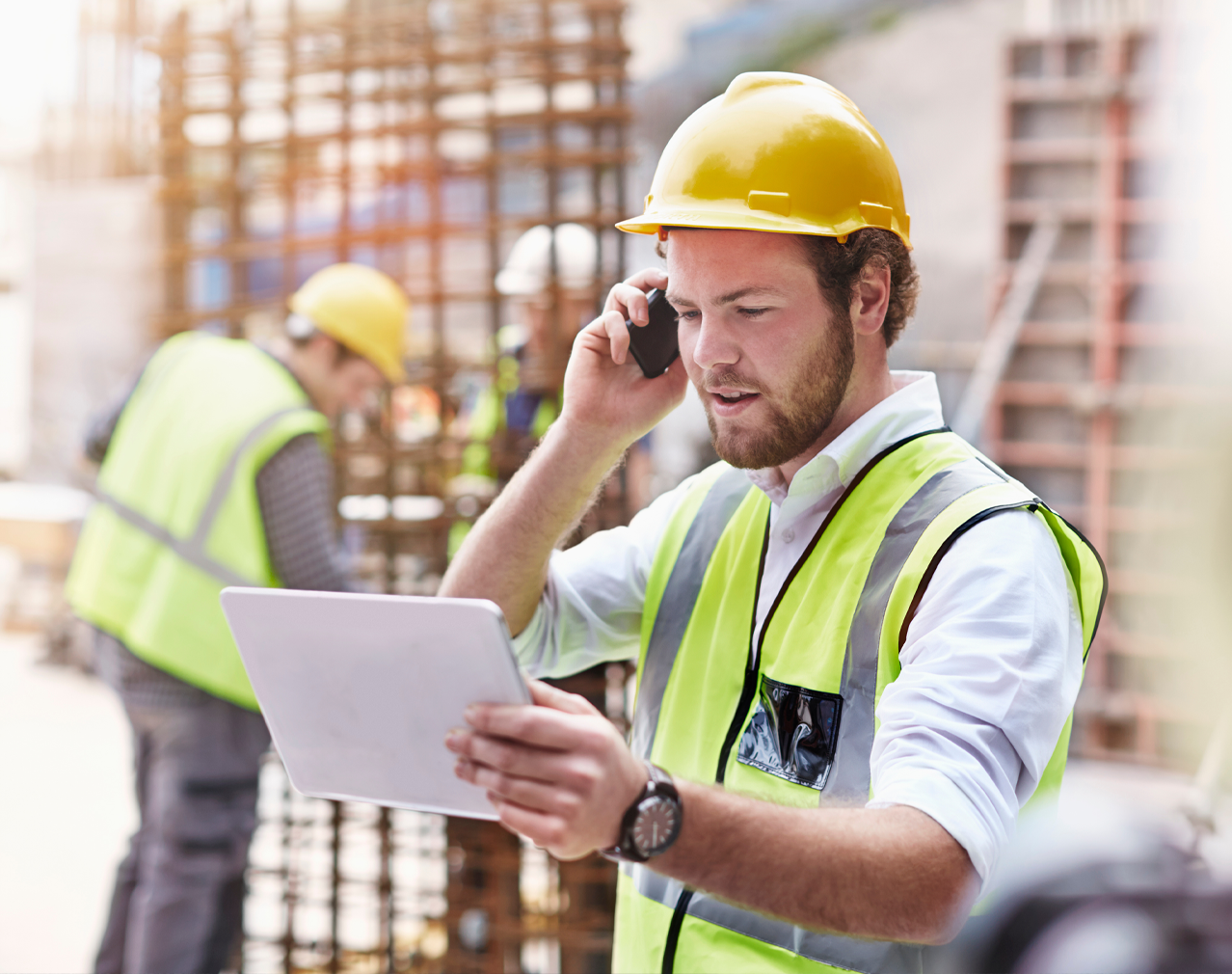
What’s the best part of working in logistics at Cordeck?
According to the team, it’s the people and the pace. They get to meet a wide range of individuals, solve new challenges every day, and stay on their toes in a very fast-paced environment. It’s a role that requires adaptability, creativity, and strong communication. Cordeck Logistics delivers all that and more.