In FLOOR Wire Management system
Our Innovative In-Floor Cellular Raceway System is an In-Slab Wire Management System That Delivers Power and Data Where You Need it.
Services
Full project management and engineering services are offered by Cordeck's expert, in-house engineering and detailing services to assure optimal planning and design.
Our experienced engineers, project managers, and sales staff provide individual customer service and attention to detail from CONCEPT to COMPLETION.
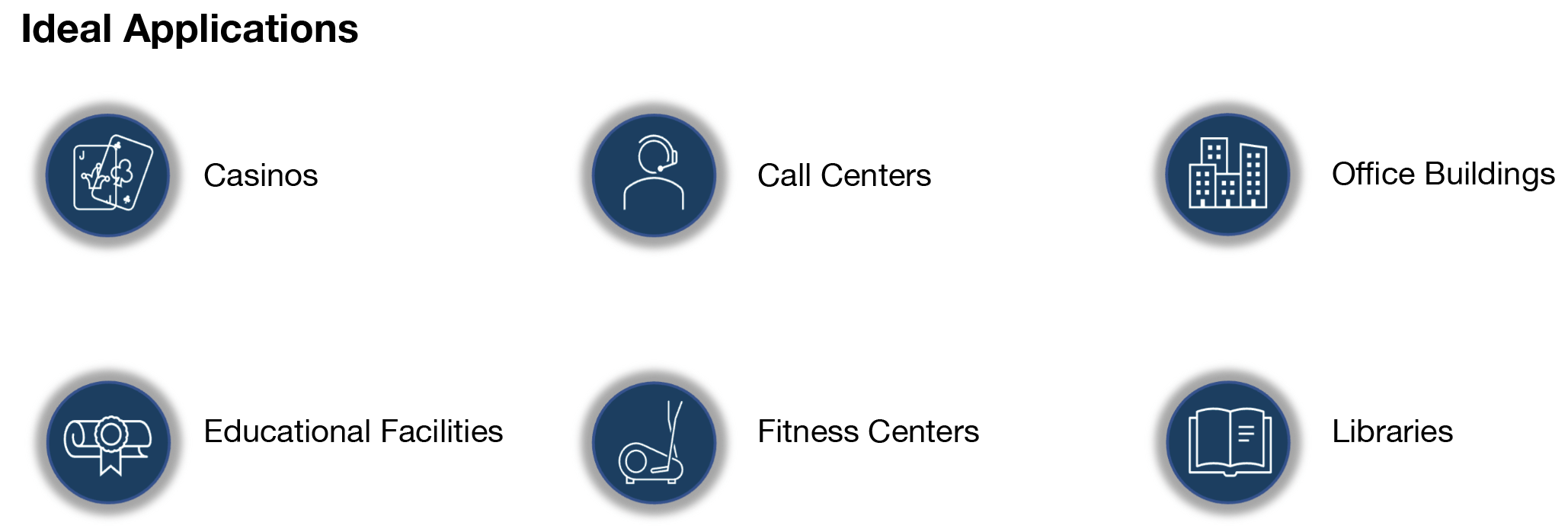